At Weito, a leading integrated manufacturing and trading company in the automotive parts industry, our expertise in ball joint production highlights our commitment to quality and precision. Below, we provide a detailed yet concise overview of our production process, demonstrating the advanced techniques and rigorous quality standards that set us apart.
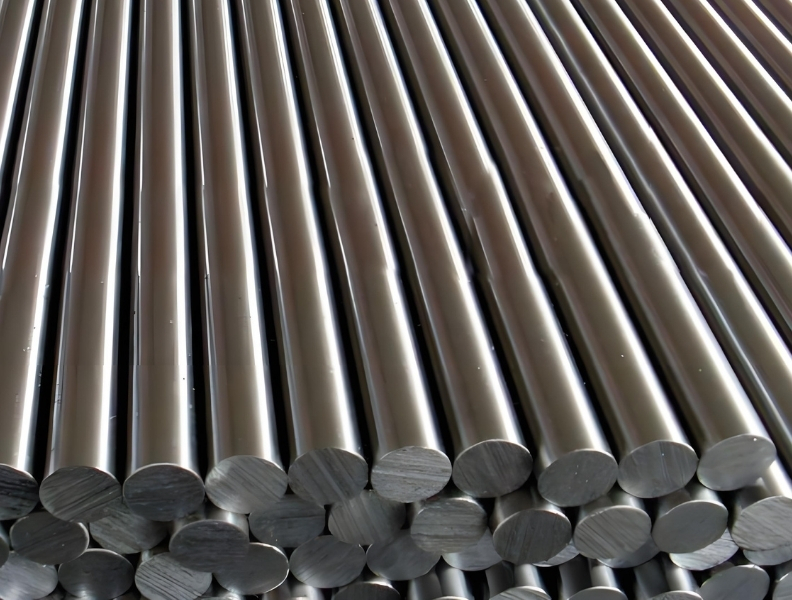
Material Selection: Strength and Reliability at the Core
We use JHSCM435 alloy steel as our raw material, chosen for its outstanding strength and durability. Guided by precise blueprints, we determine the dimensions of the ball socket and ball pin. The raw material is securely positioned on the cutting platform and cut into rough shapes with precision, forming the foundation for accurate machining.
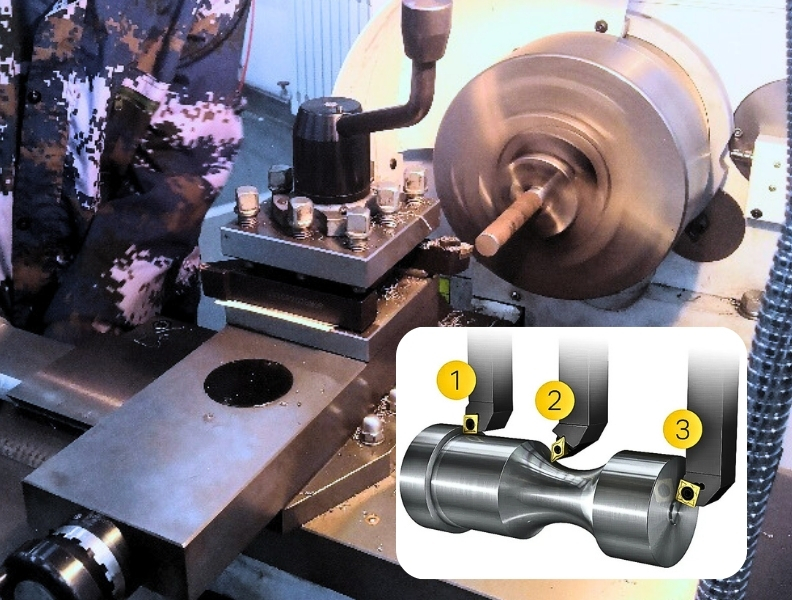
Precision Machining: Crafting the Core Components
Ball Socket Machining: The socket undergoes rough shaping followed by drilling and cutting to form the ball slot. Quality checks ensure dimensional accuracy before proceeding to the next step.
Ball Pin Machining: The ball pin is precisely shaped, cut, and ground to match the design specifications. Final checks confirm all dimensions are accurate, ensuring a flawless fit during assembly.
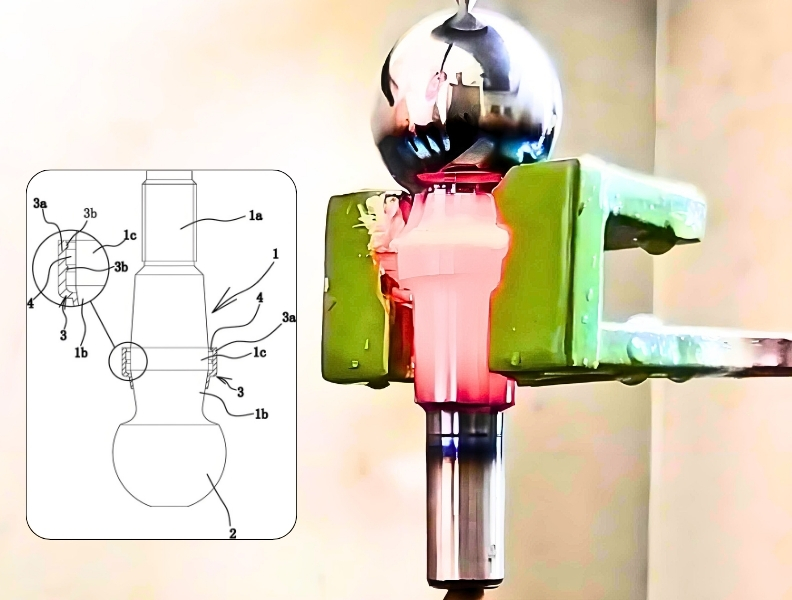
Heat Treatment: Maximizing Strength and Durability
The ball socket and ball pin are heat-treated through a controlled quenching process to enhance surface hardness and improve their material properties. This critical step ensures they can withstand the demands of suspension systems, providing longevity and reliability.
Polishing and Surface Electroplating: Refined for Performance
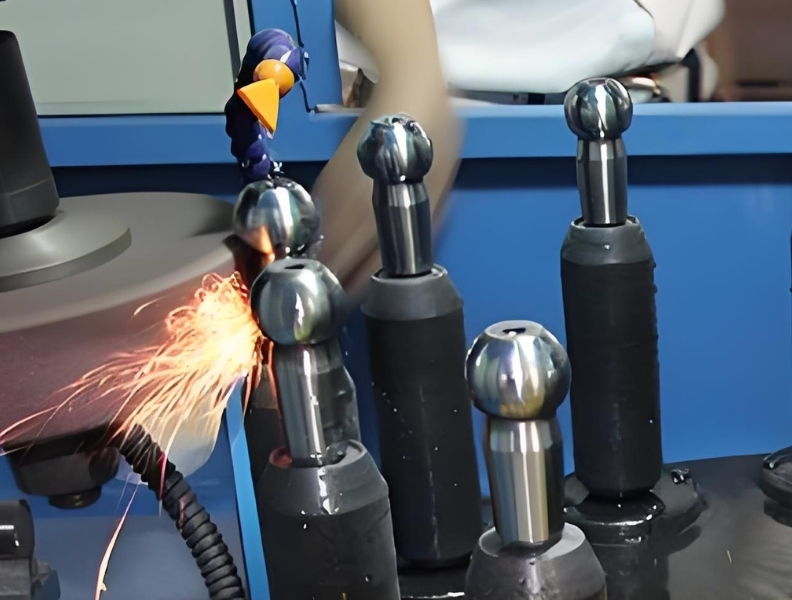
Following heat treatment, the components are polished to achieve a smooth, flawless surface. Electroplating with nickel adds corrosion resistance, improves durability, and gives the components a professional finish, ready for high-performance automotive applications.
Assembly: Achieving a Seamless Fit
After verifying the precision of the ball socket and ball pin, we heat the ball slot for thermal expansion and assemble the components. This technique ensures a secure and perfect fit, completing the ball head assembly with precision.
Salt Spray Testing: Guaranteeing Corrosion Resistance
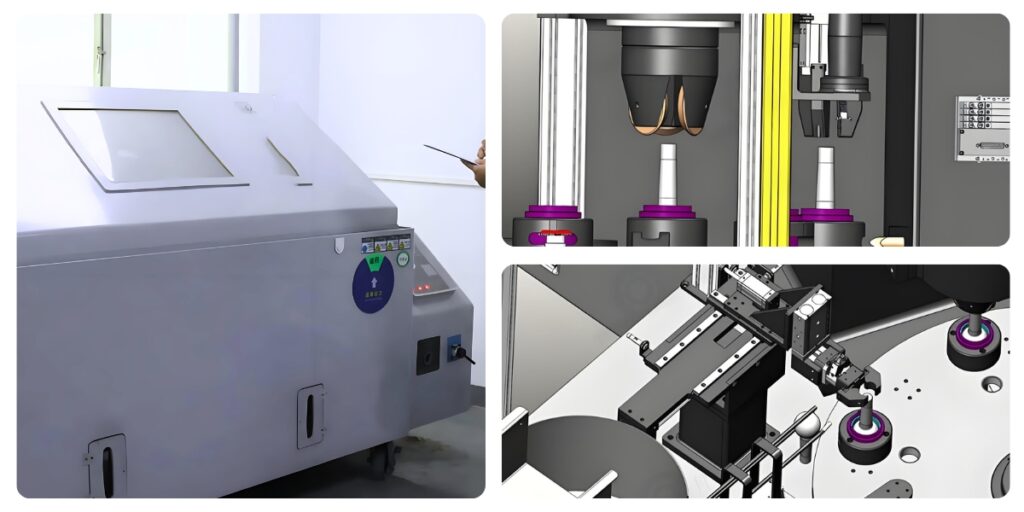
To ensure long-term performance, our suspension ball heads undergo rigorous salt spray testing:
1.Sample Preparation: Assembled samples are selected for testing.
2.Testing Procedure: A saline mist is applied to simulate corrosive environments.
3.Evaluation: The surface condition is inspected, and the corrosion resistance is recorded to ensure compliance with strict industry standards.
Final Inspection and Packaging: Delivering Quality to the Market
Every finished ball joint is visually inspected for defects such as cracks or scratches. Approved components are coated with rust-proof oil and securely packaged to preserve their quality during transportation. This meticulous attention to detail ensures customers receive products that meet the highest industry standards.